Filtration of hydraulic oils
The real problems you are giving us require real solutions. Solutions that allow you to achieve the maximum durability, reliability and productivity of your machines, while reducing maintenance costs. EOC equipment is ISO 9001: 2008 certified for their design, manufacture, ease of assembly and service. Engineers with many years of experience in this equipment segment participated in the development of these devices. We use modern technology to combat the causes of failures and try to avoid as far as possible the intervention of maintenance and repair groups. In the field of maintenance, we have radically reassessed their traditional tasks. This effort includes several goals - low maintenance costs, high productivity, low running costs, long oil life and machine parts.
Problems with contaminated oil
It is a well-known fact that in 85% of failures of hydraulic machines and circuits, contaminated hydraulic oil is the cause. Water and dirt (metal powder, dust, sawdust) reduce the original ability of the oil to form a thin oil film that ensures the machine runs smoothly. Removing these impurities results in longer machine life as well as energy savings. EOCs clean the oil so efficiently that they increase machine performance and the used oil will provide unlimited service life. EOC keeps the oil cleaner and better than new oil.
Principle
The system utilizes an electrostatic principle to remove submicro particles of insoluble impurities without affecting the soluble additives in the oil. Small-sized particles are electrostatically directed and deposited on the positive or negative electrode walls. Large particles are collected on the resin impregnated cellulose filter. Another component of the device is a dehydration filter that removes oil from the oil (up to 5000 ppm). Modern additives in oil are highly resistant to deterioration. Therefore, they can be used for a long period of time as long as we keep a clean and dry environment free from contamination.
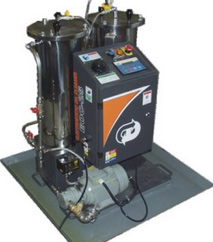

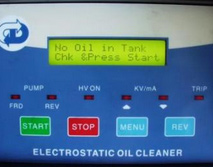
Electrostatic oil cleaners
EOC Removes:
- impurities up to 0.01 micron
- metal impurities
- non-metallic impurities
- dust and rust water in oil up to 5000 ppm
- retains impurities caused by oxidation, i. retains particles of coal, deposits, tar and varnishes
- keeps oil better than new oil, NAS 1638 grade 5-6
The EOC can:
- No additional oil change is required
- display the device status
- does not require supervision during cleaning
- Removes water
- improves the performance of hydraulic components
- removes clog-related failures (on pumps, motors and valves)
- Easy to install
- low operating costs
- reducing energy consumption
- extremely short payback time
Applications:
- injection molding machines
- Construction machines
- hydraulic presses
- Air Force
- turbine oil in hydropower plants
- measurement and cooling
- building mechanisms
- Aluminum - non-ferrous extruders
- plywood
- Servo valves controlled hydraulically
- leather processing
- mining machinery
- gearboxes
- machine tools
- automobile industry
- the steel industry
- the food industry

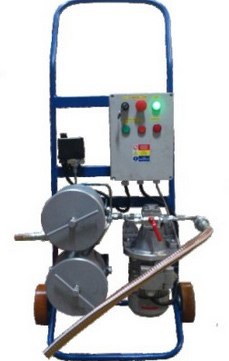
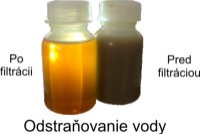
Mechanical oil cleaners
Mobile filter device DIAGO FZ - 10 and FZ-20:
The principle of this filtration is very simple. Unlike a normal full-flow filter, each bypass filter system is installed in the by-pass of the oil circuit. A small amount of oil is withdrawn from the main oil stream and passed through a filter behind which the cleaned oil is returned to the same system or to an oil reservoir. The filter emits oil free of mechanical impurities, carbon, and a considerable percentage of water.
Advantages of bypass filtration:
- prolonging the oil change interval. In hydraulic applications, oil changes almost become unnecessary.
- prolonging the life of a full-flow filter. Most contaminants are trapped by the bypass filter to prevent saturation of the full-flow filter.
- important wear reduction. The capture of particulate contaminants prevents the "sanding" effect of these particles on machine components.
- Prevent damage to machinery and system. Blocking dynamic clearances in components is removed by filtering out larger parts.
- prolong the life of the machine and reduce wear.
- Reduction of repair costs by improving the machine's proper functioning.
- Improved environmental impact through preventive maintenance and oil life extension.
The use:
- removal of mechanical impurities from 1 micrometer (dust, metal particles, carbon)
- in combination with the electrostatic EOC cleaner, it serves to remove unwanted paints (resins) from the oil. In this combination of deployments, the entire system is cleaned, as well as the already set paints on the pipe walls and the operating surfaces of the control and control components.
- removing a significant percentage of water
Laboratory to evaluate the purity of hydraulic oils
Analysis of your oil to determine its grade according to ISO 4406, NAS 1638 or GOST 17216.
Analysis of contaminated samples
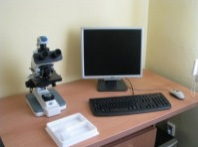
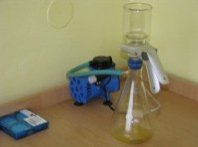
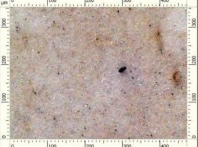
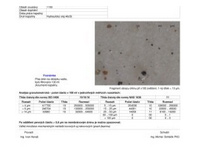
In addition to the purity class analysis, we also provide analysis of kinematic viscosity ISO 3104 and water content in oil STN EN 60841 - low-phenolic antioxidant IEC 60666.